
Advantage is taken of the positive side effects, as for example good surface quality, low deviation from concentricity and optimized alignment accuracy. In the machining world, drilling depths of 10xD and deeper are regarded as deep hole drilling operations, whereby smaller drilling depths can naturally also be produced with gun drills. Guhring – Single fluted deep hole gun drills Can easily be applied to machining centres by using a pre-drilled hole for guidance.An advantage when it is possible to use a predrilled hole instead of a drill bushing for guidance, for example in machining centres.For machining workpieces where sealing problems can occur.Adapts to existing machines, preferable in conventional lathes, turning centres, machining centres and horizontal boring machines.Requires no seal between the workpiece and the drill bushing.Requires dedicated deep hole drilling machine.When large diameter holes are required.More advantageous for long series production.In materials with an uneven structure when chip breaking problems exist.In materials with poor chip forming properties such as stainless steel, and low-carbon steel.One of the most important success factors is an effective coolant system.ĭeep hole machining is carried out using three different machining systems: Single Tube System (STS), Ejector System or by applying gun drills. Satisfactory chip breaking, and removing the chips from the cutting edge without damaging the tool or work piece, is essential. Regardless of method, the basic principles of drilling still apply, and the correct choice of cutting speeds and feeds are crucial. Rotating tool is another option as well as a combination of the two.
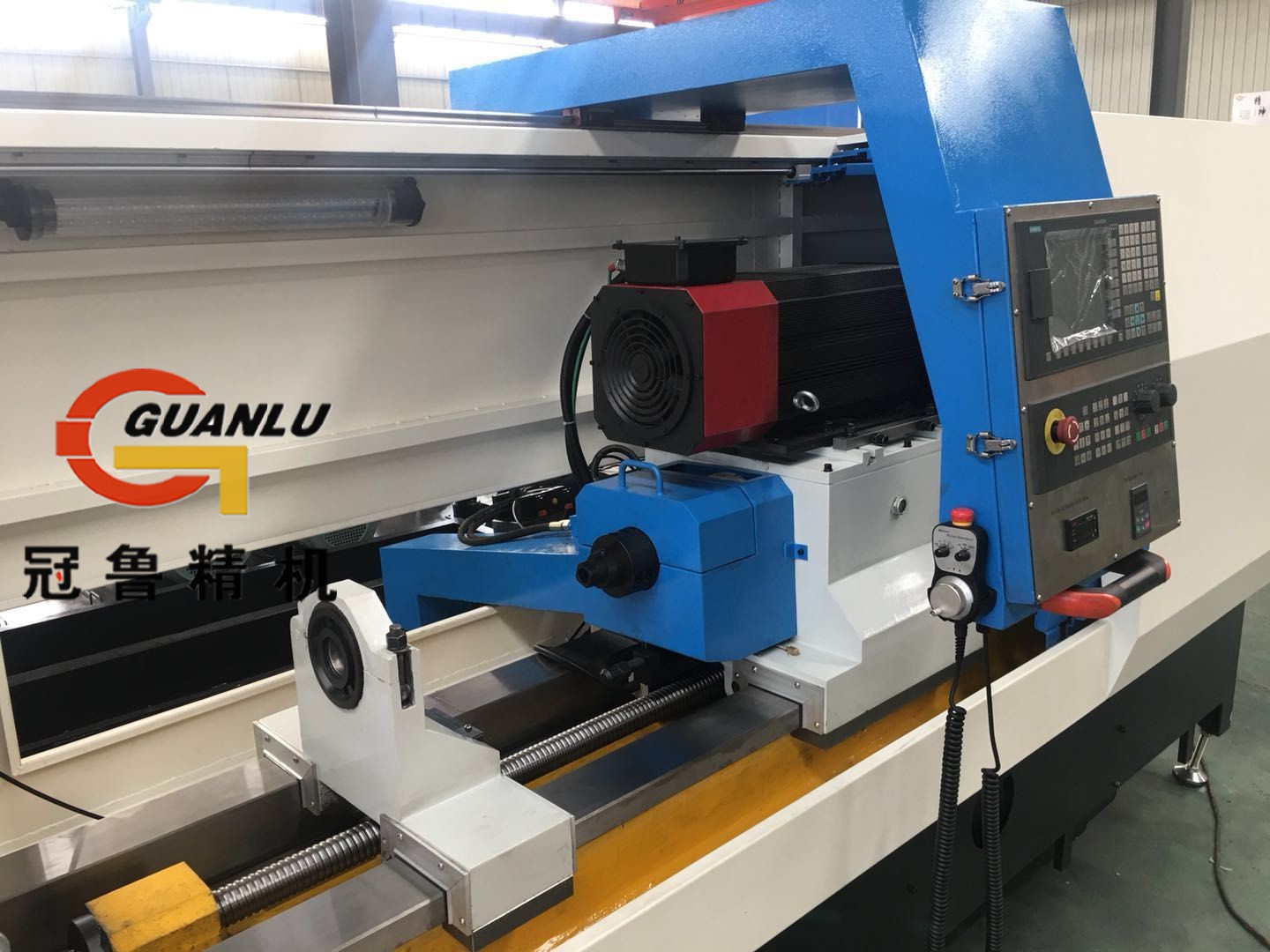
The most common method is rotating the work piece while the tool is fed in a linear movement. This can be done in different machine set-ups. Deep hole machining with Sandvik Coromantĭeep hole machining is the preferred method for drilling hole depths up to 150 x the hole diameter. Traditionally, manufacturing these components demands the use of dedicated machines, but the call for consolidated operations means a single ‘multi-task’ platform offers significant benefits to end-users. The reason for this industry trend emanates from the oil and gas, and aerospace industries, where many high value components require deep hole machining, such as valve blocks and landing gear parts. In the same way that it is possible to achieve common machining techniques such as milling, turning and gear cutting on a single machine tool platform, there is now growing demand to introduce deep hole machining to the same format.
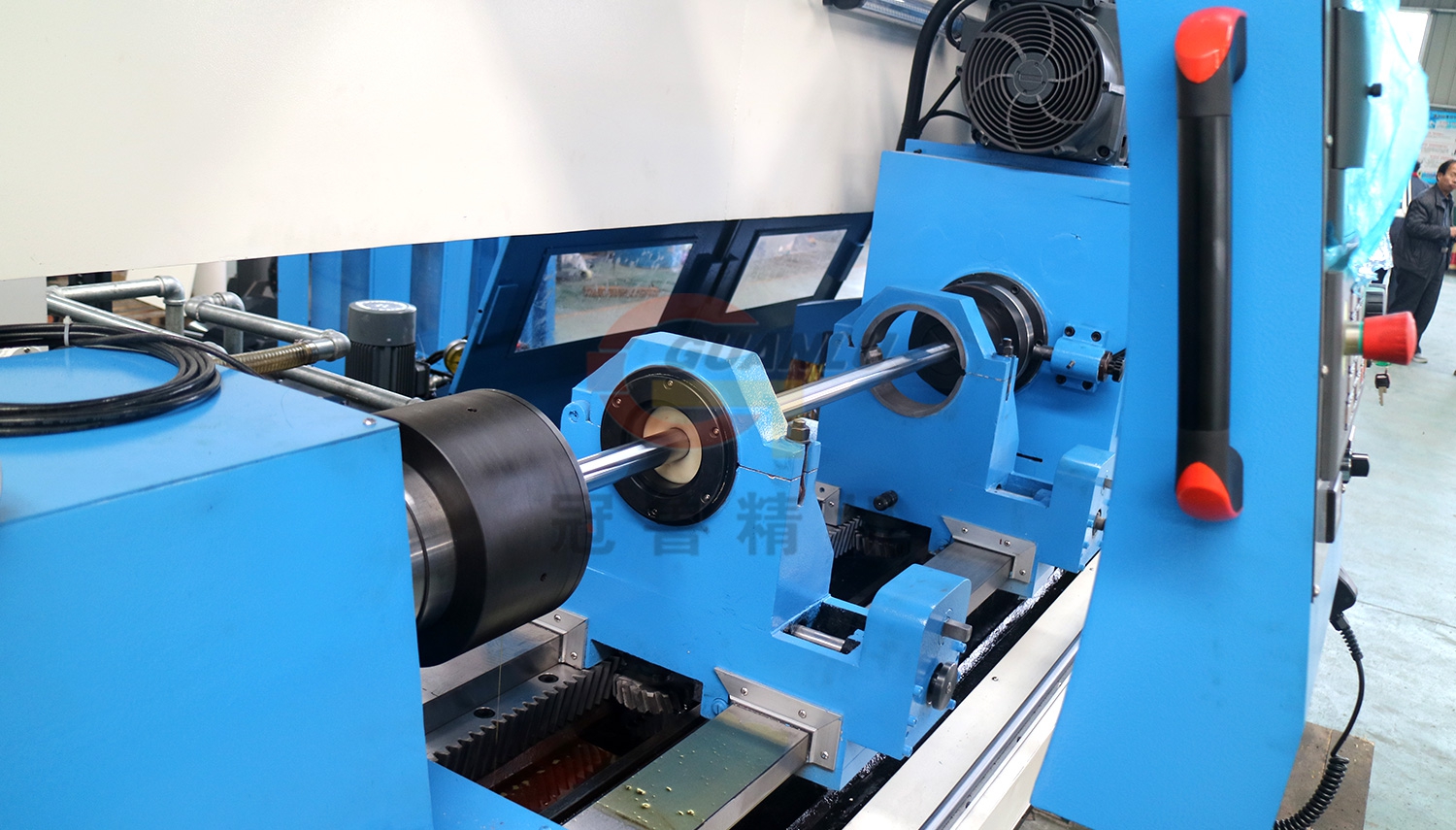
One of the most notable current trends in deep hole machining (DHM) is multi-tasking.
